Introduction
Diesel generators play a crucial role in providing backup power in various industries, commercial settings, and residential areas. Quality assurance is essential to ensure that diesel generators are reliable, efficient, and safe for use. This article will explore the importance of quality assurance in diesel generators, the key components that contribute to their reliability, and the best practices for ensuring their quality and performance.
Importance of Quality Assurance in Diesel Generators
Quality assurance is critical in the manufacturing, installation, and maintenance of diesel generators to ensure their reliable performance during power outages and emergencies. The primary function of a diesel generator is to provide backup power when the primary power source fails. Therefore, any compromise in quality can lead to significant consequences, including financial losses, operational disruptions, and safety hazards.
Reliability and performance are the cornerstones of quality assurance in diesel generators. A reliable generator should start quickly, operate efficiently, and deliver consistent power output within the specified parameters. Performance testing, component quality, and adherence to industry standards are essential aspects of quality assurance in diesel generators.
Key Components for Quality Assurance in Diesel Generators
Several key components contribute to the reliability and performance of diesel generators. Understanding these components is crucial for ensuring effective quality assurance practices.
1. Engine: The diesel engine is the heart of the generator and is responsible for converting fuel into mechanical energy. Quality assurance in diesel engines involves rigorous testing of components such as cylinders, pistons, fuel injectors, and cooling systems. Engine performance testing is essential to ensure that the engine operates within the specified power output and fuel consumption parameters.
2. Alternator: The alternator, also known as the generator head, converts the mechanical energy from the engine into electrical power. Quality assurance in alternators involves testing for voltage regulation, frequency stability, and insulation resistance. Additionally, the selection of high-quality copper wire, proper winding techniques, and robust construction are critical for ensuring the reliability of the alternator.
3. Control Panel: The control panel houses the electrical components and monitoring instruments that govern the operation of the diesel generator. Quality assurance in control panels involves testing of control circuits, voltage regulators, safety interlocks, and instrumentation accuracy. Proper wiring, insulation, and adherence to electrical standards are essential for the safe and reliable operation of the control panel.
4. Cooling System: The cooling system is vital for maintaining the optimal operating temperature of the diesel engine and alternator. Quality assurance in the cooling system involves testing for proper coolant flow, radiator efficiency, and thermal management. Additionally, the selection of high-quality coolant, pumps, and heat exchangers is crucial for preventing overheating and ensuring the longevity of the generator.
5. Fuel System: The fuel system delivers diesel fuel to the engine for combustion. Quality assurance in the fuel system involves testing for fuel filtration, injection timing, and fuel efficiency. Proper sealing, pressure regulation, and contamination control are essential for ensuring the reliable and efficient operation of the fuel system.
Best Practices for Quality Assurance in Diesel Generators
To ensure the quality and reliability of diesel generators, several best practices should be followed throughout the lifecycle of the generator, including design, manufacturing, installation, and maintenance.
1. Compliance with Standards and Regulations: Adherence to industry standards and regulatory requirements is fundamental for quality assurance in diesel generators. International standards such as ISO 8528 for generator set performance and IEC 60034 for alternator performance provide guidelines for design, testing, and performance parameters. Additionally, compliance with local codes and regulations ensures the safe installation and operation of diesel generators.
2. Quality Control in Manufacturing: Rigorous quality control measures should be implemented during the manufacturing of diesel generators. This includes material inspection, component testing, assembly quality checks, and performance validation. Quality control processes such as ISO 9001 certification, Six Sigma methodologies, and continuous improvement initiatives are crucial for ensuring the highest standards of quality in manufacturing.
3. Performance Testing and Validation: Comprehensive performance testing should be conducted on diesel generators to validate their reliability and efficiency. This includes load testing, transient response testing, fuel consumption testing, and environmental testing. Performance validation ensures that the generator meets the specified power output, voltage regulation, frequency stability, and emissions compliance.
4. Installation and Commissioning: Proper installation and commissioning are essential for the reliable operation of diesel generators. Quality assurance during installation involves site assessment, foundation design, electrical connections, and safety considerations. Commissioning activities such as startup testing, load transfer testing, and system integration testing verify the proper functioning of the generator in its operational environment.
5. Preventive Maintenance and Service: Regular preventive maintenance and service are critical for sustaining the quality and performance of diesel generators. This includes routine inspections, lubrication, filter replacements, fuel system servicing, and electrical testing. Adherence to manufacturer's maintenance schedules, use of genuine parts, and skilled service technicians are essential for maximizing the reliability and longevity of the generator.
Case Studies and Success Stories
Several case studies and success stories demonstrate the importance of quality assurance in diesel generators and the positive impact it has on various industries and applications.
Case Study 1: Hospital Emergency Power System
A hospital in a major city experienced a power outage due to a severe storm, and the backup diesel generators failed to start, resulting in critical patient care being compromised. An investigation revealed that the generators had not undergone proper performance testing and maintenance, leading to their unreliable operation during the emergency. Subsequently, the hospital upgraded to high-quality diesel generators with rigorous quality assurance processes, including comprehensive performance testing, preventive maintenance procedures, and onsite training for the maintenance staff. As a result, the new generators provided reliable backup power during subsequent outages, ensuring uninterrupted patient care and safety.
Case Study 2: Data Center Backup Power Solution
A large data center facility faced frequent power fluctuations and grid outages, causing disruptions to their critical IT infrastructure. The existing backup power system, comprising diesel generators, failed to provide seamless transition during power outages, resulting in data loss and operational downtime. The data center management collaborated with a reputable generator manufacturer to implement a customized backup power solution with a focus on quality assurance. The new diesel generators underwent extensive performance testing, including load testing, transient response testing, and parallel operation testing. Additionally, the installation and commissioning process followed strict quality control measures, ensuring proper integration with the existing electrical infrastructure. Quiet 400kW generator for industrial applications upgraded backup power solution provided reliable and seamless transition during subsequent power outages, safeguarding the data center's operations and minimizing business disruptions.
Success Story: Industrial Manufacturing Plant
An industrial manufacturing plant implemented a comprehensive preventive maintenance program for its diesel generators, focusing on quality assurance and reliability. The program included regular inspections, oil and filter changes, fuel system servicing, and electrical testing to ensure the generators were always in optimal condition. As a result, the plant experienced minimal downtime during power outages and maintained continuous production without interruptions. The proactive approach to quality assurance and maintenance of the diesel generators contributed to significant cost savings and operational efficiency for the manufacturing plant.
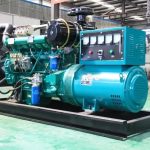
Conclusion
Quality assurance in diesel generators is essential for ensuring their reliability, efficiency, and safety in providing backup power during emergencies and power outages. Key components such as the engine, alternator, control panel, cooling system, and fuel system play a critical role in the performance of diesel generators and require rigorous quality control measures. Best practices for quality assurance include compliance with standards and regulations, quality control in manufacturing, performance testing and validation, proper installation and commissioning, and regular preventive maintenance and service. Case studies and success stories highlight the positive impact of quality assurance in diesel generators across various industries and applications. By prioritizing quality assurance, organizations can ensure the dependable operation of diesel generators and mitigate the risks associated with power disruptions.